The Jumbo Jigger dyeing machine is a cornerstone in the textile industry, known for its efficiency and effectiveness in dyeing woven fabrics.
What is a Jumbo Jigger Dyeing Machine?
A Jumbo Jigger dyeing machine is a specialized equipment used in the textile industry for dyeing fabrics, particularly woven fabrics. It operates by moving the fabric back and forth through a dye bath, allowing for consistent and uniform color application. The machine’s design facilitates high-pressure dyeing, which ensures deep penetration of dyes into the fibers.
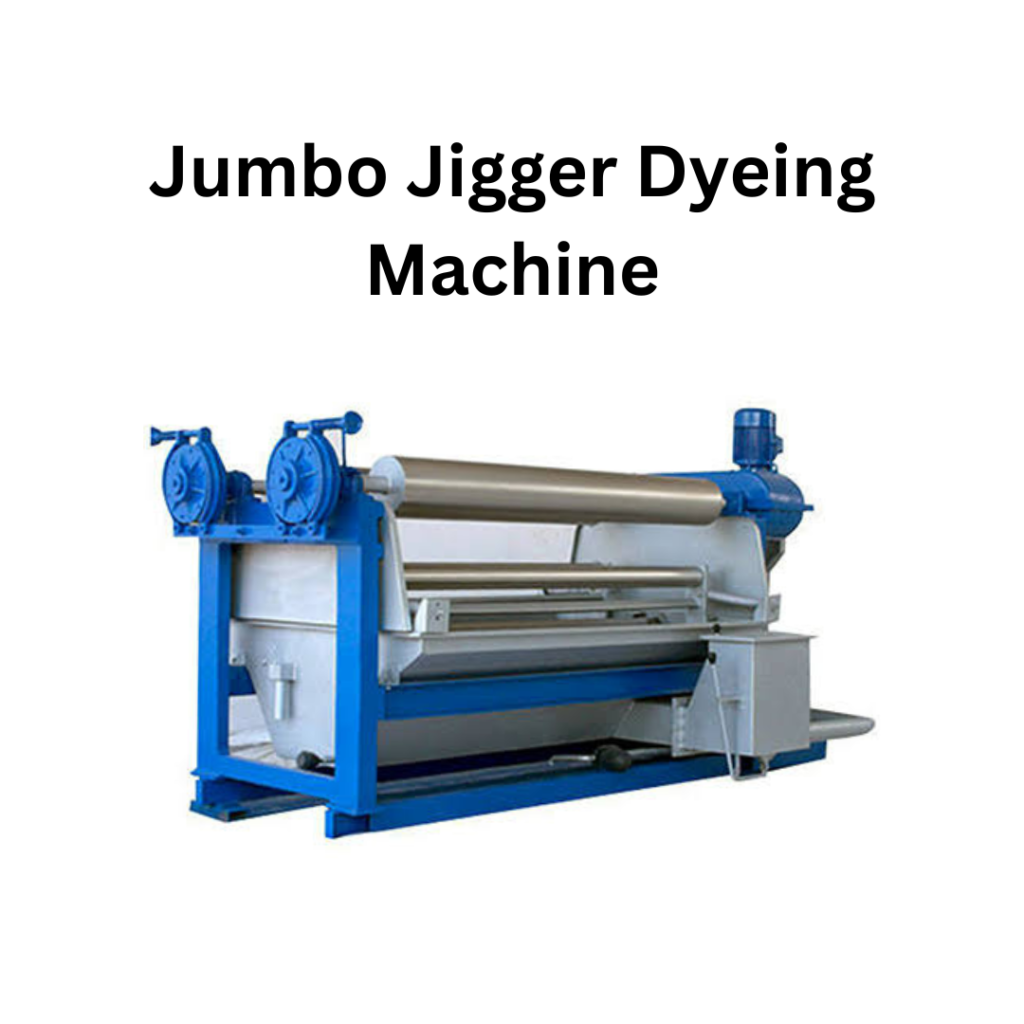
Process & Recipe
The dyeing process using a Jumbo Jigger machine involves several critical steps to ensure that the fabric is uniformly dyed and achieves the desired color fastness. Here’s an overview of the process and a typical dyeing recipe:
- Preparation of Fabric: The fabric is thoroughly cleaned and pre-treated to remove any impurities, oils, or sizing agents that might interfere with the dyeing process.
- Loading the Machine: The fabric is wound onto the main rollers of the Jigger machine. The machine can handle large volumes of fabric, making it suitable for industrial-scale operations.
- Preparation of Dye Bath: The dye bath is prepared by dissolving the dye and auxiliary chemicals in water. The specific recipe varies based on the type of fabric and dye, but a typical recipe might include:
- Dye: The primary colorant, which could be a direct dye, reactive dye, vat dye, or disperse dye.
- Salt: Enhances dye uptake by the fabric.
- Soda Ash: Used for pH control, especially with reactive dyes.
- Wetting Agents: Ensure even penetration of the dye.
- Sequestering Agents: Prevents interference from metal ions in the water.
- Setting Parameters: The machine parameters, such as temperature, speed, and pH, are set according to the dyeing recipe.
- Dyeing Process: The fabric is alternately passed through the dye bath by rotating the main rollers. This back-and-forth motion ensures that the dye is evenly distributed.
- Rinsing and Washing: After the dyeing process, the fabric is thoroughly rinsed to remove any unfixed dye and auxiliary chemicals.
- Finishing: The fabric is treated with softeners or other finishing agents to enhance its hand feel and performance characteristics.
Objects and Purposes
The primary objective of using a Jumbo Jigger dyeing machine is to achieve high-quality, uniform dyeing on woven fabrics. The purposes include:
- Ensuring deep dye penetration and excellent color fastness.
- Achieving uniform color distribution across the entire fabric length.
- Enhancing the fabric’s aesthetic and functional properties.
- Maximizing efficiency and productivity in large-scale textile dyeing operations.
Understanding and The Importance of Jumbo Jigger Dyeing
The Jumbo Jigger dyeing machine is crucial in the textile industry for several reasons:
- Consistency: The machine’s ability to maintain consistent dyeing parameters ensures uniformity in color and quality.
- Efficiency: High-pressure dyeing results in faster dye uptake and shorter processing times.
- Versatility: Suitable for a wide range of fabrics and dye types.
- Scalability: Ideal for industrial-scale dyeing operations, handling large volumes of fabric efficiently.
Different Agents Used
Various agents are used in the dyeing process to achieve desired results, including:
- Dyes: The primary colorants (direct, reactive, vat, disperse, etc.).
- Salts: Enhance dye uptake by the fabric.
- Alkali: Used for pH control.
- Wetting Agents: Ensure even penetration of the dye.
- Sequestering Agents: Prevent interference from metal ions.
- Leveling Agents: Ensure even dye distribution.
- Fixing Agents: Improve dye fastness.
Advancements in Technology
Technological advancements have significantly improved the efficiency and capabilities of Jumbo Jigger dyeing machines. Modern machines are equipped with:
- Automated Controls: For precise monitoring and adjustment of dyeing parameters.
- Advanced Sensors: To detect and correct any inconsistencies in real-time.
- Energy-Efficient Systems: Reducing water and energy consumption.
- Improved Material Handling: Enhancing the machine’s ability to handle delicate fabrics without damage.
Methods of Dyeing and Machine Types
The Jumbo Jigger dyeing machine operates primarily on a back-and-forth movement method, which ensures even dye application. There are different types of Jigger machines, such as:
- Conventional Jiggers: Basic models with manual controls.
- Automatic Jiggers: Equipped with automated systems for precise control.
- High-Pressure Jiggers: Allow for dyeing at higher temperatures and pressures, enhancing dye uptake.
Effectiveness of Jumbo Jigger Dyeing
The effectiveness of the Jumbo Jigger dyeing process is measured by:
- Uniformity: Even color distribution without streaks or patches.
- Color Fastness: Resistance to fading and bleeding.
- Efficiency: Shorter processing times and lower resource consumption.
- Quality: Superior finish and hand feel of the dyed fabric.
Method/Type of Dyeing
The Jumbo Jigger machine is primarily used for batch dyeing, where a specific quantity of fabric is dyed in a single cycle. This method is suitable for achieving consistent results across large fabric lengths.
Chemical Recipe and Chemical Benefits in the Process
The chemical recipe for Jumbo Jigger dyeing varies depending on the fabric and dye used. A typical recipe might include:
- Reactive Dye: Provides excellent color fastness and vibrancy.
- Salt: Enhances dye uptake.
- Soda Ash: Controls pH and aids in dye fixation.
- Wetting Agent: Ensures even dye penetration.
- Sequestering Agent: Prevents metal ion interference.
- Leveling Agent: Ensures uniform dye distribution.
Machine Parts
A Jumbo Jigger dyeing machine consists of several key parts:
- Main Rollers: For winding and unwinding the fabric.
- Dye Bath: Contains the dye solution.
- Drive System: Controls the movement of the rollers.
- Heating System: Maintains the dye bath temperature.
- Control Panel: For setting and monitoring dyeing parameters.
- Pumps and Valves: For circulating the dye solution.
- Sensors and Gauges: For monitoring temperature, pH, and pressure.
Parameters (Time, Temperature, pH, Speed)
The critical parameters for Jumbo Jigger dyeing include:
- Time: The duration the fabric is exposed to the dye solution.
- Temperature: The heat level of the dye bath, crucial for dye solubility and fabric compatibility.
- pH: The acidity or alkalinity of the dye bath, affecting dye-fiber interaction.
- Speed: The rate at which the fabric moves through the dye bath.
How to Start the Machine and Setup
Starting and setting up a Jumbo Jigger dyeing machine involves:
- Loading the Fabric: Wind the fabric onto the main rollers.
- Preparing the Dye Bath: Dissolve the dye and auxiliary chemicals in water.
- Setting Parameters: Adjust temperature, pH, and speed on the control panel.
- Running the Machine: Initiate the dyeing process, ensuring the fabric moves back and forth through the dye bath.
- Monitoring: Continuously monitor the process to ensure consistency.
- Rinsing and Finishing: After dyeing, rinse and finish the fabric as required.
Why Do You Do This?
Following the proper setup and operation procedures ensures:
- Quality: Achieving the desired color and fastness.
- Efficiency: Minimizing waste and resource use.
- Consistency: Uniform dyeing across the fabric.
Consequences of Improper Setup
Improper setup can lead to several issues:
- Uneven Dyeing: Streaks or patches of color.
- Poor Fastness: Fading and bleeding of the dye.
- Fabric Damage: Overheating or incorrect pH can damage the fabric.
Checking Dyeing Quality
To check if the dyeing process is done properly, chemicals such as:
- Dyebath Analysis Kits: Measure residual dye concentration.
- Color Fastness Testers: Assess resistance to washing, rubbing, and light.
Problems During Dyeing
Common problems that occur during dyeing include:
- Uneven Dyeing: Caused by improper preparation or inconsistent dye bath.
- Color Spots: Due to undissolved dye particles.
- Fabric Creasing: Resulting from improper handling.
- Low Fastness: Poor fixation of dye.
- Excessive Dye Loss: Inefficient dye uptake.
Common Defects
- Shade Variation: Differences in color intensity across the fabric.
- Patchiness: Irregular color patches.
- Streaks: Linear color defects.
- Color Fading: Loss of color intensity over time.
- Poor Hand Feel: Fabric feels rough or stiff.
Conclusion
The Jumbo Jigger dyeing machine plays a vital role in achieving high-quality, consistent dyeing in the textile industry.
Questions & Answers
- What is a Jumbo Jigger dyeing machine?
- A specialized machine for dyeing woven fabrics by moving the fabric back and forth through a dye bath.
- How does the Jumbo Jigger dyeing process work?
- The process involves pre-treating the fabric, preparing the dye bath, setting parameters, running the dyeing cycle, and rinsing the fabric.
- Why is the Jumbo Jigger machine important in textile dyeing?
- It ensures uniform dyeing, deep dye penetration, and high efficiency.
- What are the key parameters in the Jumbo Jigger dyeing process?
- Time, temperature, pH, and speed.
- What chemicals are used in the dye bath?
- Dyes, salts, soda ash, wetting agents, sequestering agents, and leveling agents.
- What advancements have been made in Jumbo Jigger dyeing machines?
- Automation, advanced sensors, energy-efficient systems, and improved material handling.
- What are common defects in Jumbo Jigger dyeing?
- Shade variation, patchiness, streaks, color fading, and poor hand feel.
- How do you start and set up a Jumbo Jigger dyeing machine?
- Load the fabric, prepare the dye bath, set parameters, start the machine, monitor the process, and rinse the fabric.
- What happens if the dyeing setup is not done properly?
- Results in uneven dyeing, poor fastness, and potential fabric damage.
- How can you check the quality of the dyeing process?
- Using dyebath analysis kits and color fastness testers to ensure proper dyeing.