Introduction
Textile printing is a vital technique in the fashion and fabric industries, transforming plain fabrics into colorful and patterned materials.
What is Textile Printing?
Textile printing is the process of applying color to fabric in definite patterns or designs. In properly printed fabrics, the color is bonded with the fiber, so as to resist washing and friction. Textile printing encompasses various methods, including screen printing, digital printing, and transfer printing, each with its unique processes and applications.
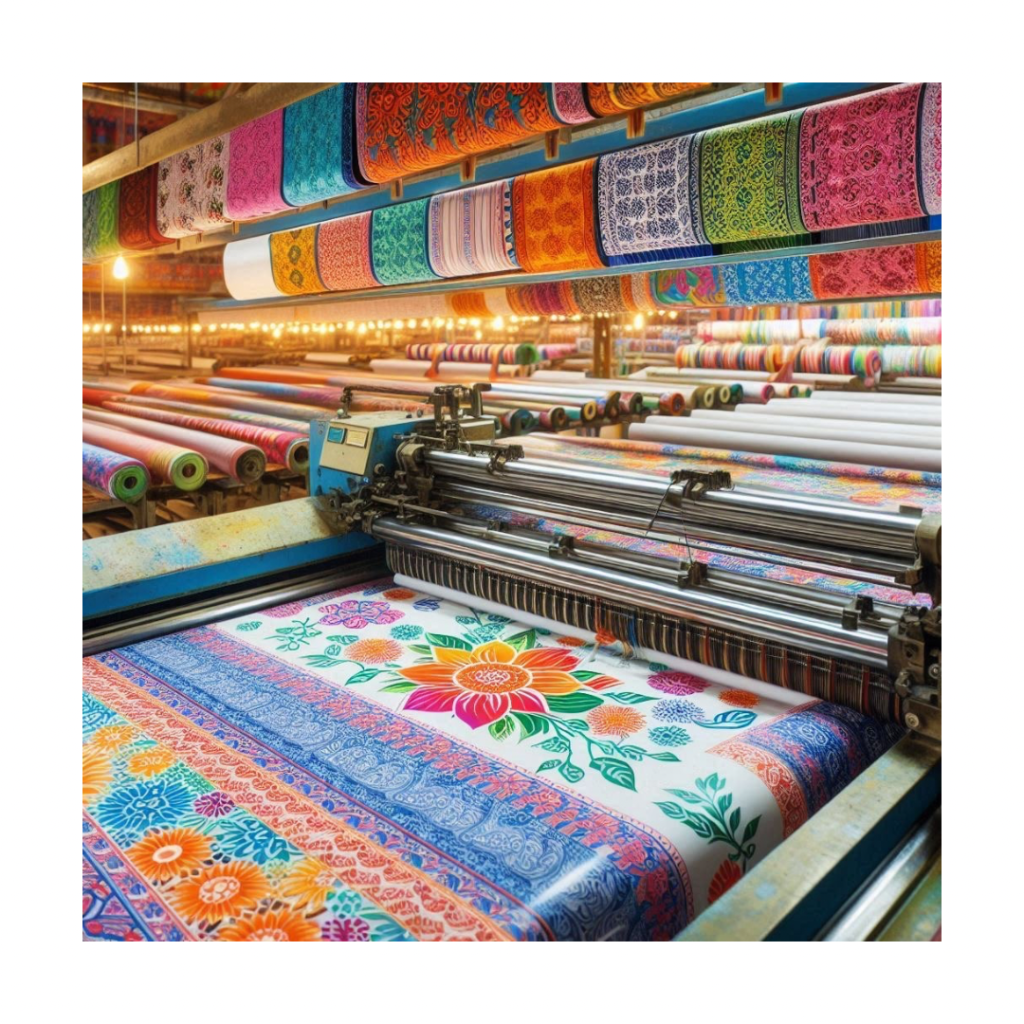
Process & Recipe
The textile printing process typically involves several stages:
- Design Creation: The first step is designing the pattern or image to be printed on the fabric. This can be done using software or hand-drawn.
- Preparation of Printing Paste: A printing paste is created by mixing dyes or pigments with thickeners, binders, and other chemicals. The recipe for the paste depends on the type of dye, the fabric, and the printing method.
- Fabric Preparation: The fabric is prepared by washing and bleaching to ensure it is clean and has a uniform surface. This step may also involve applying a pre-treatment to enhance dye absorption.
- Printing: The prepared paste is applied to the fabric using a specific printing technique, such as screen printing, digital printing, or block printing.
- Fixation: The printed fabric is then treated with heat or steam to fix the dye or pigment, ensuring it bonds with the fabric fibers.
- Washing and Drying: The fabric is washed to remove excess dye and chemicals, then dried.
- Quality Control: The printed fabric undergoes quality control checks to ensure the print is accurate and durable.
Recipe Example for Reactive Dye Printing Paste
- Reactive dye: 5-10%
- Urea: 10-20%
- Sodium bicarbonate: 1-2%
- Thickener: 3-5%
- Water: balance to 100%
Objects and Purposes of Textile Printing
The primary objective of textile printing is to create aesthetically pleasing designs on fabrics. It allows for the customization of textiles, adding value and functionality. Textile printing also serves purposes such as branding, conveying information, and enhancing the visual appeal of garments and home textiles.
Understanding and The Importance of Textile Printing
Textile printing is crucial for the fashion industry, interior design, and various industrial applications. It allows for the mass production of patterned fabrics, enabling designers to bring their visions to life. Understanding the printing process helps in selecting the appropriate method and materials, ensuring high-quality, durable prints.
Different Agents Used in Textile Printing
Various agents are used in textile printing to achieve desired effects:
- Dyes and Pigments: Provide color to the fabric.
- Thickeners: Give the printing paste the right consistency.
- Binders: Ensure pigments adhere to the fabric.
- Fixing Agents: Enhance the bond between the dye and fabric.
- Auxiliaries: Include wetting agents, dispersing agents, and defoamers to improve the printing process.
Advancements in Technology
Technological advancements have revolutionized textile printing. Digital printing, for instance, allows for precise, high-resolution prints with minimal waste. Innovations in ink formulations and fabric treatments have also improved the quality and durability of printed textiles.
Methods and Machines
Methods
- Screen Printing: Uses a stencil to apply ink on the fabric through a mesh screen.
- Digital Printing: Employs inkjet technology to print designs directly onto the fabric.
- Block Printing: Involves hand-carving designs onto blocks and stamping them onto the fabric.
- Heat Transfer Printing: Transfers designs from paper to fabric using heat and pressure.
Machines
- Rotary Screen Printing Machine: Uses cylindrical screens to print continuous patterns.
- Flatbed Screen Printing Machine: Uses flat screens for printing on fabric.
- Digital Inkjet Printer: Directly prints digital designs onto fabric.
- Heat Press Machine: Applies heat and pressure to transfer designs from paper to fabric.
Machine Parts
- Screen (in screen printing): Mesh stencil that holds the design.
- Squeegee: Spreads the printing paste over the screen.
- Print Head (in digital printing): Dispenses ink onto the fabric.
- Heat Plate (in heat transfer printing): Provides heat and pressure for transferring designs.
Parameters
Time, Temperature, pH, and Speed
- Time: Depends on the method and fabric; typically ranges from seconds to several minutes.
- Temperature: Critical for dye fixation; can range from 100°C to 200°C.
- pH: Affects dye performance; typically kept neutral or slightly acidic/alkaline.
- Speed: Varies with machine type and fabric; high-speed machines can print several meters per minute.
Starting and Setting Up a Printing Machine
- Prepare the Fabric: Ensure it is clean and pre-treated.
- Load the Design: Upload the design to the machine’s control system.
- Prepare the Printing Paste: Mix dyes, thickeners, and other chemicals according to the recipe.
- Set Machine Parameters: Adjust time, temperature, speed, and other settings.
- Run a Test Print: Check the print quality and make adjustments if needed.
- Start Production: Begin the printing process, monitoring quality continuously.
Why Do You Do This?
Setting up the machine properly ensures consistent print quality, reduces waste, and maximizes production efficiency. Proper setup also minimizes defects and rework, saving time and costs.
Consequences of Improper Setup
Improper setup can lead to issues such as color inconsistency, blurred designs, incomplete prints, and fabric damage. These defects can reduce the fabric’s marketability and increase production costs due to rework and wastage.
Checking for Proper Printing
Fixation Test: Use a chemical such as sodium carbonate to check dye fixation. Properly fixed dyes will resist washing and show minimal color loss.
Problems During Textile Printing
Common problems include:
- Color Fading: Poor dye fixation or improper washing.
- Blurring: Excessive printing paste or improper screen tension.
- Smudging: Wet prints coming into contact with each other.
- Patchiness: Uneven application of printing paste.
- Misalignment: Poor registration of multi-color prints.
Minimum 5 Common Defects
- Color Bleeding: Dyes spreading outside the intended design.
- Pinholes: Small, unprinted areas due to air bubbles in the printing paste.
- Ghosting: Faint, unintended prints from residual paste.
- Double Printing: Overlapping prints due to fabric movement.
- Surface Cracking: Printed design cracking on the fabric surface after drying.
Conclusion
Textile printing is a dynamic and intricate process that requires careful attention to detail and an understanding of various techniques and materials to achieve high-quality, durable designs.
Questions & Answers
- What is textile printing?
Textile printing is the process of applying color to fabric in specific patterns or designs. - What are the main steps in the textile printing process?
Design creation, preparation of printing paste, fabric preparation, printing, fixation, washing and drying, and quality control. - What are the common methods of textile printing?
Screen printing, digital printing, block printing, and heat transfer printing. - What advancements have been made in textile printing technology?
Innovations include digital printing, improved ink formulations, and enhanced fabric treatments. - What is the role of thickeners in textile printing?
Thickeners give the printing paste the right consistency for application. - Why is proper machine setup important in textile printing?
It ensures consistent print quality, reduces defects, and maximizes production efficiency. - What can happen if the printing machine is not set up correctly?
Issues like color inconsistency, blurred designs, and fabric damage can occur. - How can you check if the dye is properly fixed to the fabric?
Use a fixation test with a chemical such as sodium carbonate. - What are some common defects in textile printing?
Color bleeding, pinholes, ghosting, double printing, and surface cracking. - What is the significance of temperature in the printing process?
Temperature is critical for dye fixation, influencing the bond between dye and fabric fibers.